LASER SCANNING FOR HIGH-ACCURACY DATA CAPTURE
Data capture with 3D scanning is efficient, flexible, and highly accurate. What can we scan? From the face of a penny to the contours of a fighter jet — and everything in between. We leverage a variety of scanning technologies as needed to address constraints of material, size and complexity.
CMM Scanning, Continuous Contact, Touch Probe & Hard Probe
Coordinate Measuring Machines (CMMs) are mechanical systems that use a measuring transducer technology to convert probe and physical measurements of an object’s surface into electrical signals that are then analyzed by specialized metrology software. There are many different types of CMMs. The most basic systems use hard probes and XYZ read-outs, while the most complex employ fully automated continuous contact probing.
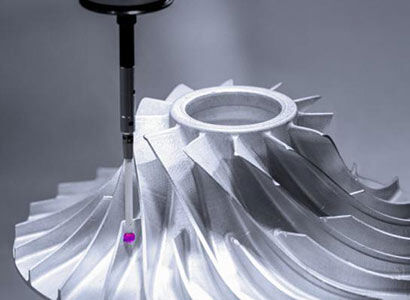
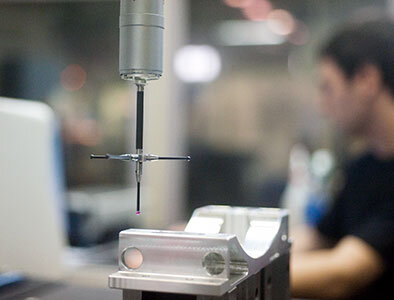
Talk To An Expert
Don’t see exactly what you are looking for? Or maybe you do and want more specifics or an estimate. Either way, you can call us at
470-264-5765
right now or just fill out the form below and we will respond back within 24 hours.
Optical CMM Scanning
Some applications call for a portable solution, for example taking measurements on a shop floor or in the field. In these cases an Optical CMM can be used to gather measurement data for areas that are difficult to reach. The hand-held device transmits data wirelessly and allows the operator to move both the part and the scanner during the measuring process. Using stereoptics to scan an object, the Optical CMM uses 2-3 cameras to track either passive retroreflective or active targets through space. This process allows objects to be rebuilt in 3D via the device’s reflectors.
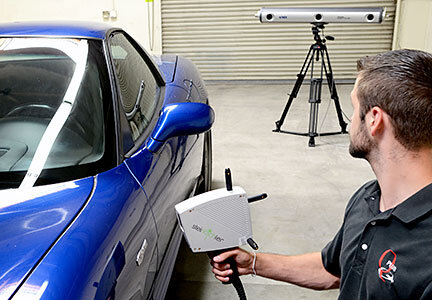
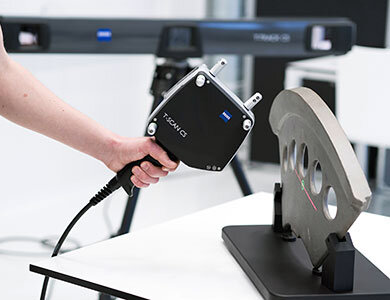
Articulated Arm Scanning
An articulating arm is a type of CMM that uses rotary encoders on multiple rotation axes instead of linear scales to determine the position of the probe. These manual systems are not automated, but they are portable and can reach around or into objects in a way that cannot be accomplished with a conventional CMM to perform 3D inspections, tool certifications, CAD comparison, dimensional anlaysis, reverse engineering, and more.
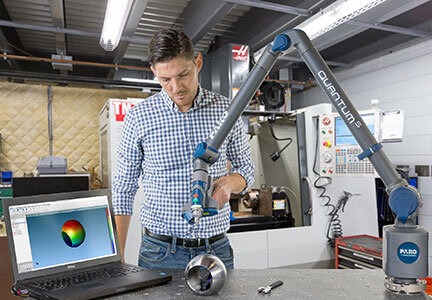
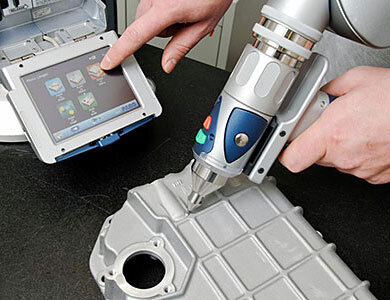
Digital Contour Tracing
Form and contour tracers are purpose-specific devices that use extremely accurate, continuous contact sensors and styli to obtain small-part geometry. These devices are especially useful for scanning objects that include threaded, cylindrical, or rounded features.
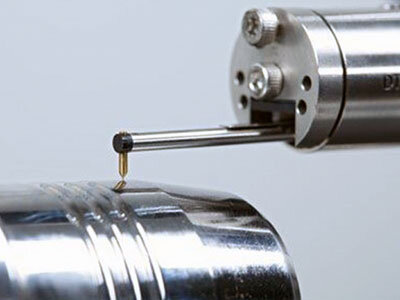
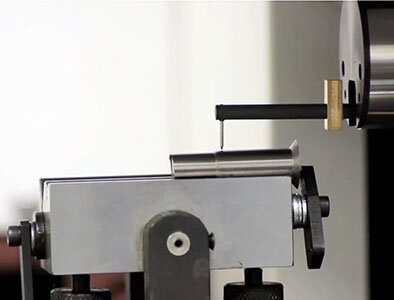
Range Scanning
Range Scanning is a type of laser scanning using a time-of-flight laser rangefinder based on LiDAR technology to measure the distance between the laser and the object’s surface. The laser rangefinder sends a pulse of light to the object and measures the amount of time it takes for the reflection to return in order to calculate the distance of each point on the surface.
Point measurements are taken by aiming the device at the object and using a series of mirrors to redirect the light from the laser to different areas on the object. Although the process may seem cumbersome, typical time-of-flight 3D laser scanners can collect between 10,000 and 100,000 points per second, which is much faster though less accurate than contact sensors.
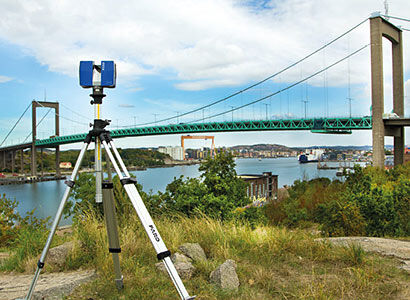
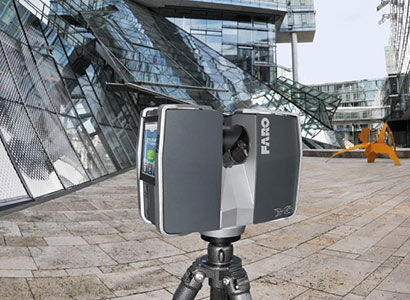
Resources
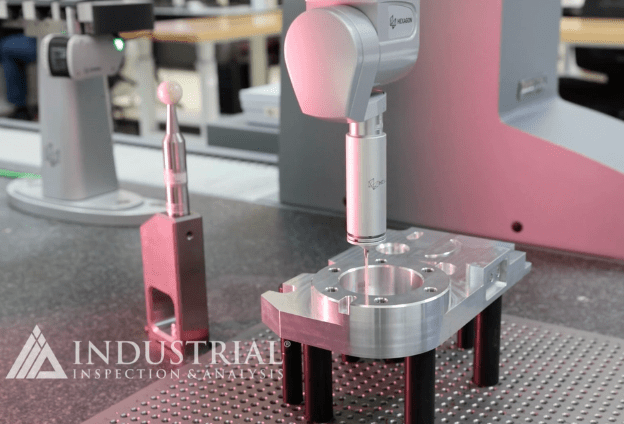
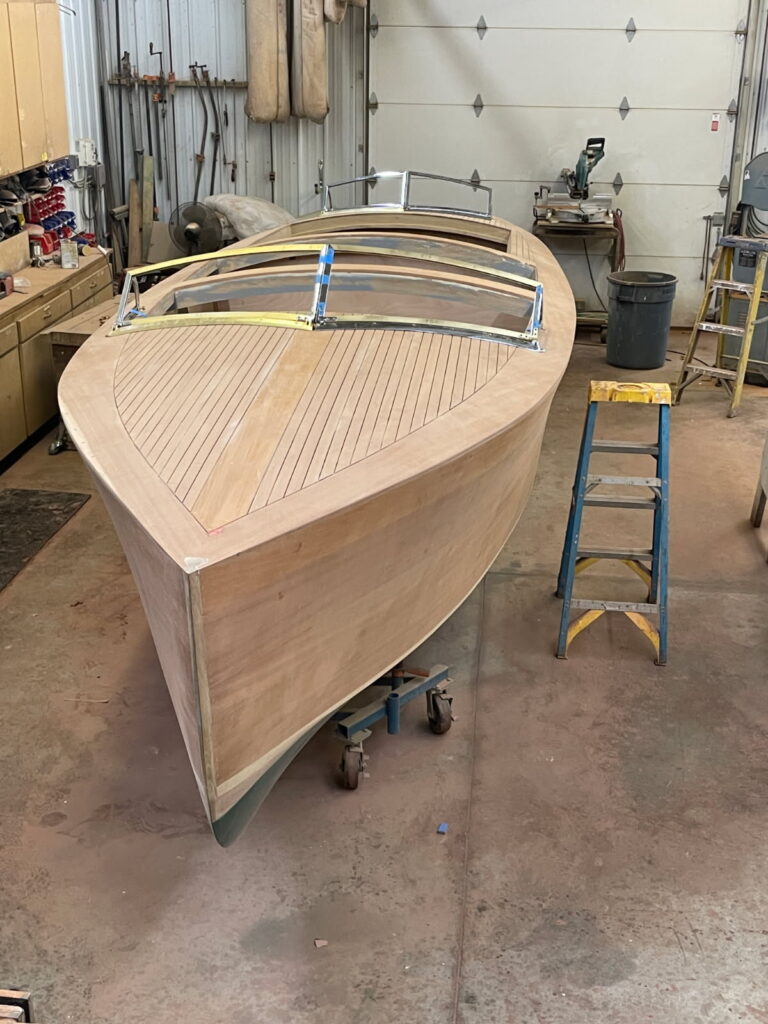
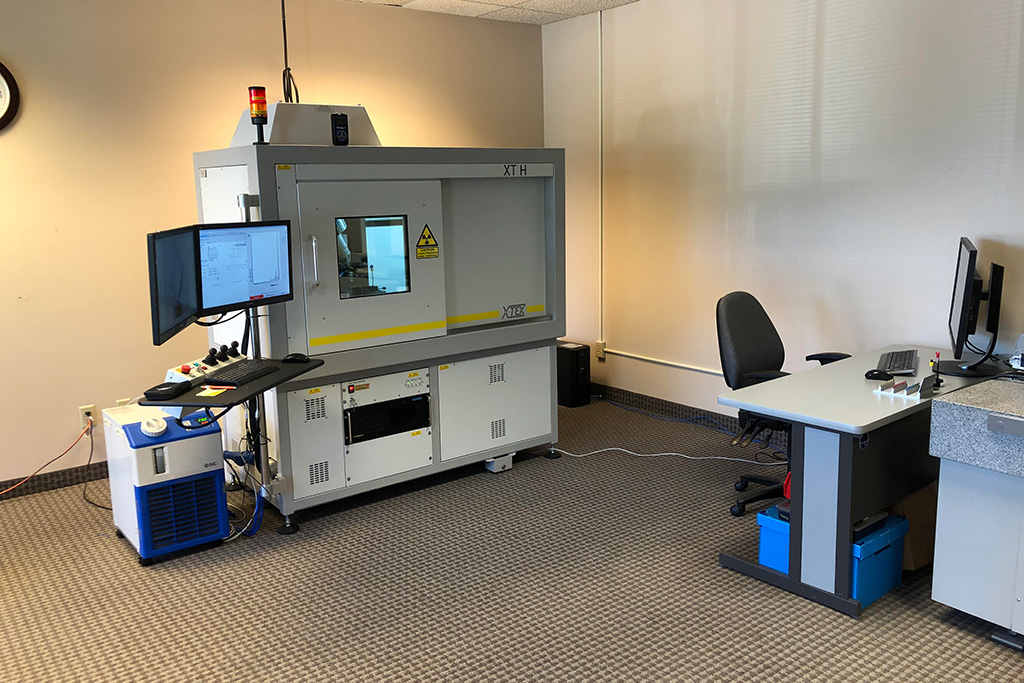