Know Your Equipment Inside & Out Non-Destructive Examination/Evaluation (NDE) Services
Whatever your industry, the safety, integrity, and reliability of parts, products, components, equipment and materials are key to your success.
The NDE Experts
In addition to practical experience, our professionals have in-depth knowledge of all applicable codes and standards — knowledge that helps keep you in compliance. Our one-stop-shop services mean fast turnaround times and cost-effective solutions for our customers. When you partner with IIA, you gain access to a vast network of skilled technicians and licensed engineers, specialized inspection tools, lab facilities and a commitment to quality.
Talk To An Expert
Don’t see exactly what you are looking for? Or maybe you do and want more specifics or an estimate. Either way, you can call us at 470-552-8301
right now or just fill out the form below and we will respond back within 24 hours.
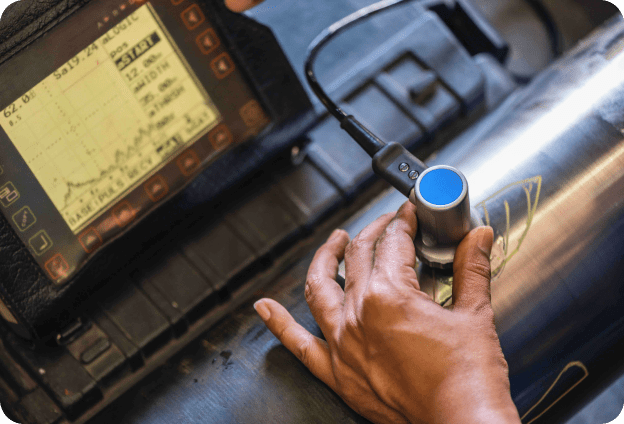
Inspection Services
IIA’s multiskilled technicians arrive on site with cutting-edge technology and a remote support network to support daily inspection needs, as well as planned maintenance activities. Our field service personnel are capable of performing inspections using traditional and specialty NDE. We also offer complete lifting solutions for overhead and mobile cranes, fire/ladder trucks, bucket trucks, deicers, and many other lift devices.
Advanced NDE services
Automated Corrosion Mapping (Internal)
This advanced ultrasonic technique uses an automatic scanner to assess the thickness of pipelines, pressure vessels and other critical equipment. The technology allows us to precisely map out and measure internal areas of corrosion.
Automated Corrosion Mapping Laser Profilometry (External)
For areas that cannot be accessed for manual examination, laser profilometry can be used to scan the surface of an object and quantify exterior roughness or cracks. This approach collects more data points and provides multiple views for analysis that can be helpful in determining if an indication is corrosion or a manufacturing defect. This inspection technique can increase the probability of detection and reduce inspection times from hours to minutes.
Computed Radiography (CR)
IIA uses the smallest, lightest CR system designed specifically for non-destructive testing. Using direct input from mobile X-ray technicians, CR greatly increases the speed and efficiency of testing, while maintaining high levels of image quality and sensitivity. Images are processed in seconds, expediting weld approval and clearance. Images may be exported for immediate auditing or imported into CAD drawings for package detailing.
Full Matrix Capture (FMC)
This portable phased array ultrasonic testing technique provides more complete and reliable data by capturing every possible transmit-receive combination for a given transducer. FMC can improve inspection speed and accuracy and minimize the need for re-scans.
GUIDED WAVE TESTING (GWT)
Using rapid remote ultrasonic screening, guided wave testing identifies changes in a component’s cross section that could result in external and/or internal defects. This corrosion detection method is ideal for screening significant lengths of metallic pipelines or other hard-to-access areas in a pipeline system. Unlike conventional ultrasonic systems, GWT is capable of assessing areas several hundred feet away from the transducer.
PHASED ARRAY UT (PAUT)
This advanced method of ultrasonic testing is used to determine component quality and detect flaws in manufactured materials, such as welds. In addition, PAUT can be effectively used for wall thickness measurements in conjunction with corrosion testing. This NDE technique can be deployed manually or automated, and it is minimally invasive, highly flexible, and offers multiple applications.
PULSED EDDY CURRENT ARRAY (PECA)
Pulsed eddy current array is a highly accurate technique to determine average wall thickness for any material that conducts electricity. PECA is best used as a screening technique; other methods are better suited for detecting isolated areas of corrosion.
CONVENTIONAL UT (SHEAR WAVE)
Primarily used for weld inspections, shear wave testing uses a probe to direct ultrasonic beams toward the weld at an angle. This advanced testing technique is often required for inspections involving awkward weld geometry or where a weld crown or bead is present.
TIME OF FLIGHT DIFFRACTION (TOFD)
This advanced technique is a sensitive and accurate nondestructive method used primarily to identify weld defects with extreme angles. TOFD is also effective in improving sizing accuracy of weld defects and detecting discontinuities such as cracks, lack of fusion and lack of penetration.
Conventional NDE services
Dye Penetrant (PT)
This widely applied and low-cost inspection method is used to locate surface-breaking defects in all non-porous materials, such as metals, plastics, or ceramics. PT is used to detect casting, forging and welding surface defects such as hairline cracks, surface porosity, leaks in new products, and fatigue cracks on in-service components. IIA is capable of performing all types and methods of penetrant inspection.
Magnetic Particle (MT)
Magnetic particle inspection (MT or MPI) is an inspection method for locating surface or shallow sub-surface defects on ferromagnetic material, such as castings, forgings, welds and machined parts. IIA can perform both wet and dry MPI methods. There is essentially no limit to the size and shape of parts that can be inspected using MT.
Visual Testing (VT)
With a keen eye for detail, our highly trained and certified inspectors meticulously perform visual inspections to identify indications such as cracks, corrosion, erosion, and damage. They assess the overall structural integrity of various equipment, including tanks, steam turbines, fans, pressure vessels, piping, lift equipment, and more, ensuring safety and reliability in high-stress environments.
Radiography (RT)
Radiographic testing accurately detects internal defects in welds, castings, and parts used in high-stress or high-reliability environments. Conventional radiography, using gamma sources, is popular in many industries for its accuracy, cost-effectiveness, portability, and flexibility. IIA provides x-ray/gamma ray/radar inspection, both film and digital, adhering to MIL-SPEC, ANSI, ASTM, and ASME standards. This testing often complements penetrant or magnetic particle inspection for surface analysis and can inspect steel thicknesses up to 3.0 inches.
Ultrasonics (UT)
Ultrasonic testing uses high-frequency sound waves to detect defects or characterize materials. It helps assess material condition and structural integrity by analyzing how sound waves travel through an object. A common application is ultrasonic thickness testing (UTT), which measures material thickness to check for corrosion. IIA offers both contact and immersive UT, including pulse echo, transmissional, straight beam, angle beam (shear wave) testing, and advanced phased array techniques.
Other Services
- Advanced / Traditional Bell Hole Examinations
- Encoded Phased Array Weld Examination (Code Compliance)
- Post-Weld Heat Treatment
- Corrosion Mapping
- Ferrite Testing
- Hardness Testing
- NDE Training
- Positive Material Identification (PMI)
- Program & Procedure Development
- Proprietary Technologies
- Phased Array Sectorial Scanning PASS® Valve Examinations
- Absolute Recordable Manual Ultrasonic Testing (ARMUT®)
- Precision Ultrasonic Testing
- Remote Visual Inspections (RVI)
- Weld Quality Inspection
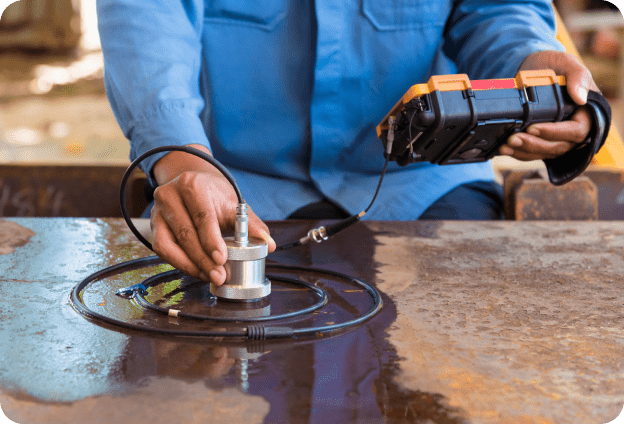
Inspections Led by Level III Professionals
Top Five Benefits of an IIA Inspection
- Creates a safe environment for your workers (prevents injury and loss of life)
- Ensures efficiency of your equipment
- Reduces repair costs
- Minimizes down time, eliminates unforeseen incidents
- Avoids costly insurance claims
Consulting
Safety & Quality Are Absolute Priorities
IIA's unrivaled support to our customers is a result of more than three decades of industry experience applying NDE to pressure vessels and piping systems. From the earliest stages in manufacturing to the investigation of component failures, IIA offers a broad range of expertise.
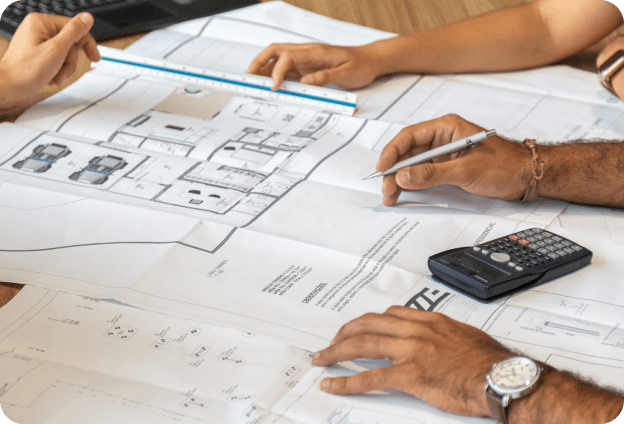
Certifications & Guidelines
All Certifications Based on Guidelines in SNT-TC-1A and CP189
Texas Department of State Health Services – Radioactive Materials Licensing (MC 2835)
New Mexico Environment Department Radioactive Material License
In Line Inspection Validation
American Welding Society
Pressure Equipment Directive 2014/68/UE (European Certification)
Pressure Equipment Regulations 1999
ASNT Level III
IRRSP
Resources
Additional Resources
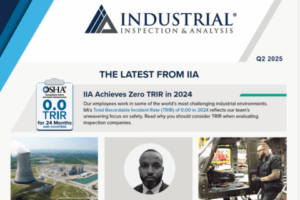
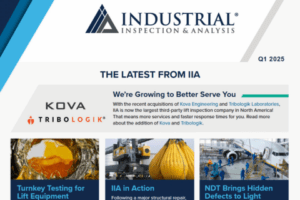
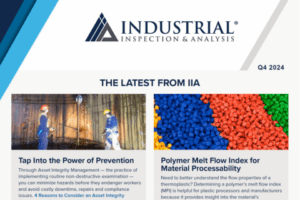