IIA’s experts offer a full range of coating testing to provide you with the fastest and most accurate results.Coating Testing
Coating testing is a critical part of the evaluation process when reviewing components and materials for safety, compliance, and durability.
Our lab experts can conduct simulated/accelerated exposure and physical testing to ensure that your product's coating can stand up to extreme environments, impact, or abrasion. We have the capability to test a wide variety of components, from small screws to large housings and electric motors. You can count on our lab experts to know exactly what testing methods should be used for your project.
Talk To An Expert
Don’t see exactly what you are looking for? Or maybe you do and want more specifics or an estimate. Either way, you can call us at
470-264-5765
right now or just fill out the form below and we will respond back within 24 hours.
Request a test
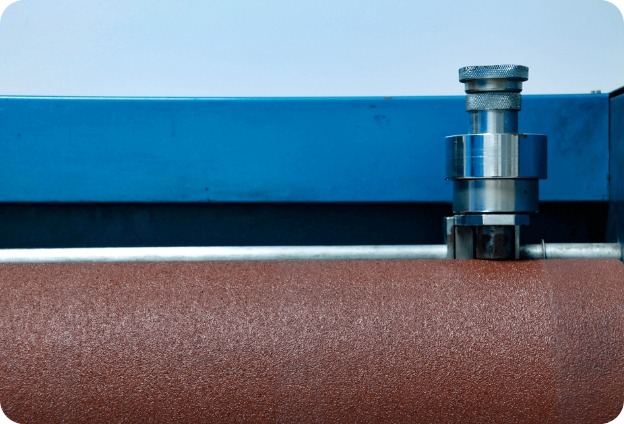
Our Services
Chemical Resistance Testing
Chemical Resistance Testing is an efficient way of assessing the ability of a protective coating to resist degradation, for example blistering, softening, or discoloration. We provide tests to evaluate plastics and coatings to determine their resistance to a variety of chemicals. Our team of trained and certified experts deliver fast, reliable testing services with accurate results for a variety of Chemical Resistance tests, including Salt Spray and Cure Testing.
Salt Spray
We provide accelerated corrosion testing by subjecting target parts to a controlled neutral salt fog, typically over a period of 1 to 2 weeks. This technique is especially important for the aerospace and automotive industries. We provide salt spray testing for aluminum components, and we also test galvanized and painted steel panels to determine the long-term resistance to corrosion.
Scanning Electron Microscopy (SEM) / Energy Dispersive Spectroscopy (EDS)
We also use a variation of Non-Destructive Testing (NDT) methods to determine which chemical elements are present on or within a sample surface, and we can also estimate the element’s relative abundance.
Abrasion Testing
IIA offers a variety of Abrasion Tests, such as Tabor Abrasion, Chip Resistance, and Peel Testing. Since friction is a common factor in degradation and deterioration of materials, our experts work diligently to help make certain your materials are safe, compliant, fit-for-purpose and as long-lasting as possible. Abrasion testing offers data to assist in predicting a product or material’s life expectancy. We test to the requested standards and deliver findings regarding scratch resistance in relation to a specific environmental condition. We also provide Coating Hardness Testing for metallic coatings, and for non-metallic coatings, such as paint, primers, and powder coats.
Abrasion Testing (Tabor)
Friction can be the cause of deterioration of materials and abrasion testing offers information on material or coating comparisons. The data can help categorize a material’s scratch abrasion resistance, based on lab-created circumstances, and can help determine the life expectancy of the material.
Military Coating Certification - MIL-A-8625F and MIL-DTL-5541F
IIA tests and certifies the performance requirements of anodized coatings on aluminum panels to salt spray/fog.This includes salt spray corrosion resistance, coating weight, electrical resistance, coating thickness, abrasion resistance and more. We use other specifications, such as A-A-208D and A-A-59383 to determine the quality of paint and ink and our testing methods cover color, opacity, hiding power, resistance to smearing and reagents, as well as long term storage..
Cathodic Disbondment Testing & Dielectric Breakdown Testing
We provide CD Testing in conjunction with other tests to determine the long-term strength and performance of barrier coatings, specifically for oil and gas pipelines, and we provide Dielectric tests for electronic devices to help determine the device’s insulating barrier durability. Our labs test the level of resistance to voltage, which ensures compliance, safety from harmful electrical currents, and fitness-for-use.
Coefficient of Friction
IIA provides Coefficient of friction (CoF) testing for all types of materials from common ceramic tiles to films and lubricants. This test determines the material’s frictional characteristics. The results typically indicate the ease with which any two material surfaces slide against the other. An equation is then used to determine the Coefficient of Friction, which is then used to indicate, on a ratio scale of how smooth a surface is. For example, the lower the CoF, the smoother the surface.
Certifications and Guidelines
- ISO 17025:2017